We all have encountered ‘N’ numbers of construction, industrial, and many other businesses living in the office, and Unquestionably, steel plates and hardware like Nuts, Bolts, Washers, etc. is one of the most common materials in use. As bare steel surfaces are always prone to corrosion because they contain iron that oxidizes when exposed to oxygen hence there must be some provision for rust prevention and which is generally required by and of the purchaser or customer. Sometimes, the same is also specified in Technical annexures or specifications of the particular product or Item as an agreement between manufacturer and purchaser.
There are many methods for Rust prevention, However, in some cases, Zinc plating is preferable as per manufacturers’ or Purchasers’ choice.
Now the question which comes to mind is What should be the minimum coating thickness and what should be clearly specified in the Technical documents to achieve the particular coating thickness as there are various methods for zinc plating?
let us discuss the Zinc plating (also known as Galvanization) methods and their specific definition so that same can be clearly mentioned in the Technical specification or contract.
What is Galvanization?
Galvanization is a process in which a layer of Zinc is added to the surface of steel parts or hardware to prevent corrosion by preventing corrosive species from reaching the metal surface. Zinc, being more anodic than iron, becomes a sacrificial anode and prevents corrosion of the underlying steel. Galvanization is attractive in the industry because of its low cost compared to its benefits i.e long life, high reliability, group protection, etc.
How Galvanization prevents corrosion?
Zinc coating over the metal is exposed to the atmosphere and combines with oxygen in the moist atmosphere to produce zinc oxide(ZnO). As the air found in the atmosphere also contains water particles, zinc reacts with water particles to produce zinc hydroxide[Zn(OH)2]. Further, in the same way, the zinc hydroxide combines with carbon dioxide (CO2) present in the atmosphere to produce a sealed and insoluble grey layer of zinc carbonate (ZnCO3) which sticks to the zinc beneath thereby protecting it from rusting.
Various methods of Galvanization?
- Electrogalvanization
- Hot-dip galvanization
- Thermal spray Galvanisation
Electrogalvanization
This uses the basic concept of Electrolysis that we all have gone through during our school days.
This process involves the use of a sacrificial zinc anode suspended in a Zinc salt solution and Electric current. The complete setup for the Electrogalvanising consist of a Zinc anode attached to the positive side of the power source while the steel to be galvanized is attached to the negative side of the power source. When an Electric current is passed through this setup, the positively charged zinc ions given off by the Zinc anode are attracted toward the negatively charged steel.
It may be noted that zinc coating by this process is more permanent than the other processes such as Hot dip Galvanisation, Spray methods, etc. as the zinc actually adheres to the steel at a molecular level rather than being merely a coating added to the surface of the steel.
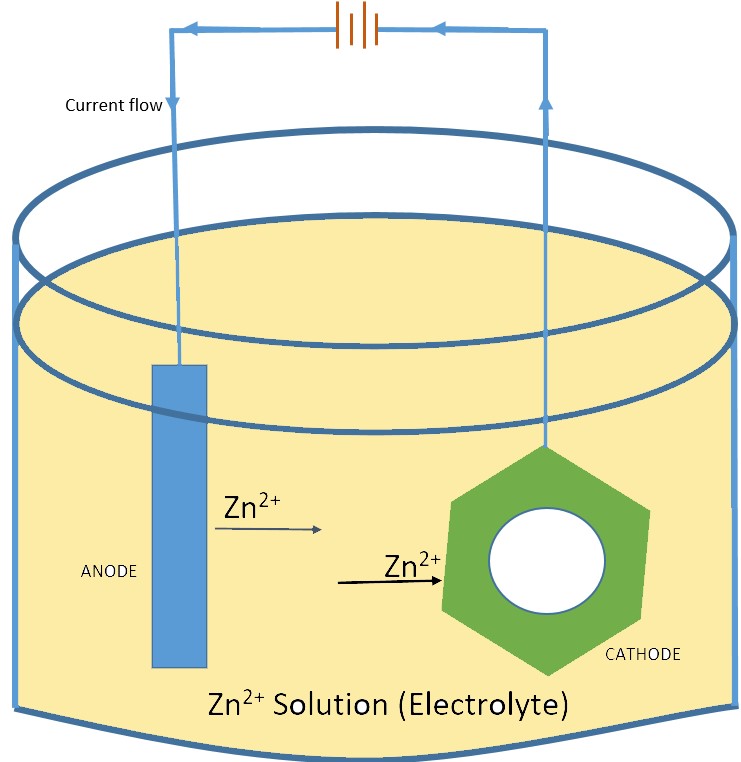
Anode and Cathode in Electrogalvanising
In Electro galvanizing, The Anode is the Positive electrode, and the Cathode is the Negative electrode. The cathode is the electrode where the Electrochemical reduction reaction occurs. The Anode is where the Electrochemical oxidation reaction occurs.
How does Electrogalvanising occur?
To understand the process let’s refer to the above Sample image, the Zinc metal (Anode) when provided with direct current, gets oxidized and dissolves its metal atoms in the electrolytic solution. At the Nut Material (Cathode), The dissolved ions of the Zinc are reduced and plated on the Nut material.
Factors affecting Electrogalvanising
- The voltage level of current.
- Temperature and chemical composition of the Electrolyte
- Duration of the current flow.
- Distance between the cathode and the anode.
Limitations of Electrogalvanisation
- Pollution Prone: The waste products left out after the process can severely damage the environment if they are not properly disposed of. Proper waste management is required.
- cost for a complete setup for apparatus is very high
- Time-consuming Process: As the layer of metal is deposited very slowly it takes a longer time than any other process. Especially when Products need multiple layers.
- Electroplating generally yields the least thickness.
- Not suitable for Product for outdoor application.
- Ideal for small components
- Low life expectancy
Advantages of Electrogalvanisation
- Uniform coating
- Cheaper initial cost
- Shiny finish
Hot-dip Galvanisation
Hot Dip Galvanization is a process of zinc plating, where a cleaned Steel or Iron is immersed into a bath of molten zinc having a temperature of around 450 degrees Celcius, and a series of zinc-iron alloy layers are formed by a metallurgical reaction between the iron and zinc, thus providing a robust layer of over the steel or Iron as an integral part of the steel.
Steps for Hot-Dip Galvanization
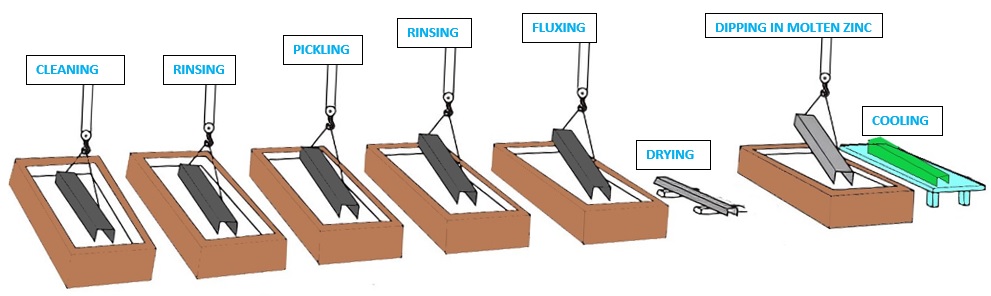
Hot-dip galvanizing process normally involves two fundamental steps i.e. Surface preparation and then Galvanising.
Surface Preparation
The basic purpose of surface preparation in any of the galvanizing processes is to obtain the cleanest possible steel surface by removing all of the oxides and other contaminating residues. Thorough surface preparation is compulsory as the reaction will only occur on a chemically cleaned surface. The good quality of zinc coating can be achieved only after proper surface preparation. For the surface preparation, The steel or Iron object goes through a series of three cleaning stages i.e Degreasing, Pickling, and Fluxing.
Cleaning or Degreasing: For cleaning purposes, the steel object is first immersed in a degreasing bath such as an alkaline caustic solution. After ensuring the cleaning, the object is rinsed with water to rinse off the degreasing agent.
Pickling: The steel is then dipped into a dilute solution which is either Hydrochloric or sulfuric acid, which removes oxides and mill scale from the surface of the Steel or Iron object. Once all oxides and mill scale is removed, it is again rinsed with water and sent to the final stage of the surface preparation.
Fluxing: Finally, the steel is dipped in the tank of flux which is slightly acidic, and contains a combination of zinc chloride and ammonium chloride at around 65-80°C. The basic purpose of the fluxing is to clean the last traces of oxides from the steel surface, which may have developed since the pickling of the steel, and to give a protective coating to prevent any further oxidation before dipping into the galvanizing Tank. It is then left for drying prior to Galvanizing.
After the surface preparation, the surface of the steel is near-white, clean, and completely free of any oxides or other contaminants that might inhibit the metallurgical reaction between iron and molten zinc in the galvanizing tank.
Galvanization
Following the surface preparation, an Iron or steel component is immersed into the tank having molten zinc. The purity of the molten zinc is maintained at around 98% and the same is generally kept at a temperature of around 450°C. A series of layers of the zinc-iron alloy is formed by a metallurgical reaction between iron and zinc. it may also be noted that the rate of reaction between the steel and the zinc is normally parabolic with time hence the initial rate of reaction is very rapid and considerable agitation can be seen in the tank having molten zinc. The major thickness of the coating is achieved during this period only. The reaction slows down with time and the coating thickness can not be increased significantly even if the steel or Iron is in the tank for a longer period of time. Generally, the typical time of immersion is about four or five minutes however, it can be longer for heavy steel structures having higher thermal inertia or where the penetration of zinc is required in large internal spaces.
Upon withdrawal of the steel structure from the galvanizing tank, a layering of molten zinc can be seen on the top surface of the steel. further, this cools to exhibit the bright shiny appearance of the Galvanised steel.
Limitations of Hot-dip Galvanisation
- The galvanizing plant is a must for Hot dip galvanizing. Application at the site if required is not possible.
- The requirement of any specific color cannot be met, External painting over zinc coated surface is the only solution.
- Dimensional constraint: The size of the structure or component is limited by the size of the zinc tank. sometimes it leads to the unavailability of the zinc tank for a specific size of the structure.
- Risk of warp of the structure due to the higher temperature of the molten zinc. However, this can be taken care of by a good design or by the cold galvanizing process.
The advantages of Hot-dip Galvanisation
- Lower initial cost: Hot dip galvanizing generally has the lowest initial cost when compared to other comparable rust preventive coatings for steel.
- Lower maintenance results in lower long-term cost
- Longer life Expectancy: Generally the life of hot dip galvanized coatings on steel members is in excess of 50 years in most rural environments and in between 10 to 30 years in most corrosive areas and coastal environments.
- Better Adhesion: Adhesion is much better as the hot dip galvanized coating is metallurgically bonded to the surface of the steel.
- Environment friendly
- Lesser time-consuming: The application of one full coating can be completed in minutes.
- Toughness: As hot dip galvanized coating has a unique metallurgical structure, it gives outstanding resistance to mechanical damage during transport and handling, erection, and service.
- Unwanted graffiti can easily be removed: Painted graffiti can be easily removed by solvents as it doesn’t damage the hot dip galvanized coating.
Thermal Spray Galvanisation
Thermal spraying galvanization, or Zinc metal spraying, is a surface coating process where zinc metal in the form of powder or wire is heated to its melting point without boiling away, and then this molten zinc is accelerated to strike on a substrate with very high velocity. Further, it is allowed to freeze onto the substrate.

Steps to spray galvanization process
- Surface preparation: The first step of spray galvanization is surface preparation just like in the other methods of galvanization as explained above. This is done by cleaning and Grit or Shot blasting the surface to be galvanized. Sometimes masking techniques are adopted for components that are having specific areas for galvanization.
- Melting: The second step is to melt the Zinc material; this is done by introducing the Zinc material into the hot gas stream which is produced by either a chemical reaction (Combustion) or by physical reaction (Plasma).
- Striking: In the third stage, Zinc particles are accelerated with high velocity to the surface of the component by the gas stream.
- At last, it is allowed to freeze to form the coatings followed by assessment for quality by either mechanical or microstructure evaluation.
Advantages of Thermal Spray Galvanization
- Thermal spray produces the thickest coating of zinc out of all the other methods of galvanization.
- Most of the components can be easily galvanized with negligible distortion.
- No site constraint for the Galvanisation
Limitations of Thermal spray galvanization :
- Thermal spray galvanization does not always indicate the characteristics of the original material
- Low degree of adhesion (spray efficiency) on small substrates and substrates with small curvature.
- Difficult to evaluate a testing method for assessing how well the coating has adhered to the substrate.
- Extra care is needed to combat noise, light, dust, fumes, and other issues.
- Difficult, or impossible, to coat inner surfaces of small diameter bores and other non-accessible surfaces
- Health and safety issues of operators are a concern because of the involvement of powder, dust, and fume. It also uses flammable gases, including acetylene, requiring safe storage.
Deciding factors of Zinc coating thickness:
This is a general misconception that a Higher thickness of zinc coating leads to better performance. And hence, deciding the minimum required coating thickness on any steel product is a measure concern for most users. Generally, the coating thickness depends on the end-user of the products. The following conditions may be considered for deciding the coating thickness.
- Environmental conditions of the products: The Environments like construction work where scaffolding tubes are more frequently used and the same is exposed to contact and hence abrasion due to handling together with sand, concrete, and similar substances used. Sand particles generally have a higher hardness than zinc, which can scratch the surface. Concrete and other substances during construction is having a negative impact on galvanized surfaces, due to their acidic, or alkaline properties in concrete’s case. Due to the above reasons, a higher zinc coating thickness shall be applied.
- Tolerance considered during the design stage: This must be considered during zinc plating, as in the case of Bolts and nuts where the size of the thread is of higher importance from matching points of view.
Life of Zinc coating in various climatic conditions:
Zinc is considered rust-free and hence used in almost all steel products as corrosion-resistant. However, it has been observed that zinc also corrodes slowly in various environments. The thickness of the zinc coating determines the duration of protection. It’s a general assumption that the thicker the zinc coating, the longer the expected life of the steel products.
In atmospheric conditions, a linear relationship is observed between the thickness of the zinc coating and the life expectancy. And hence it is possible to predict, how the thickness of the coating will behave in a particular environment, and when the initial maintenance of the product will be required. To do this, let us refer to the corrosion categories as mentioned in the table below.
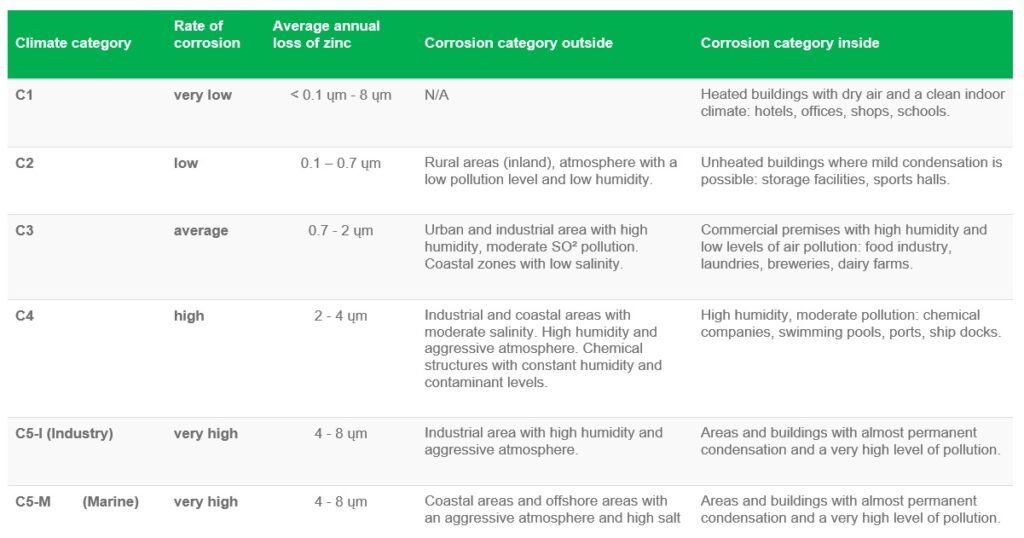